Core Tenets of Industrial MEP Design
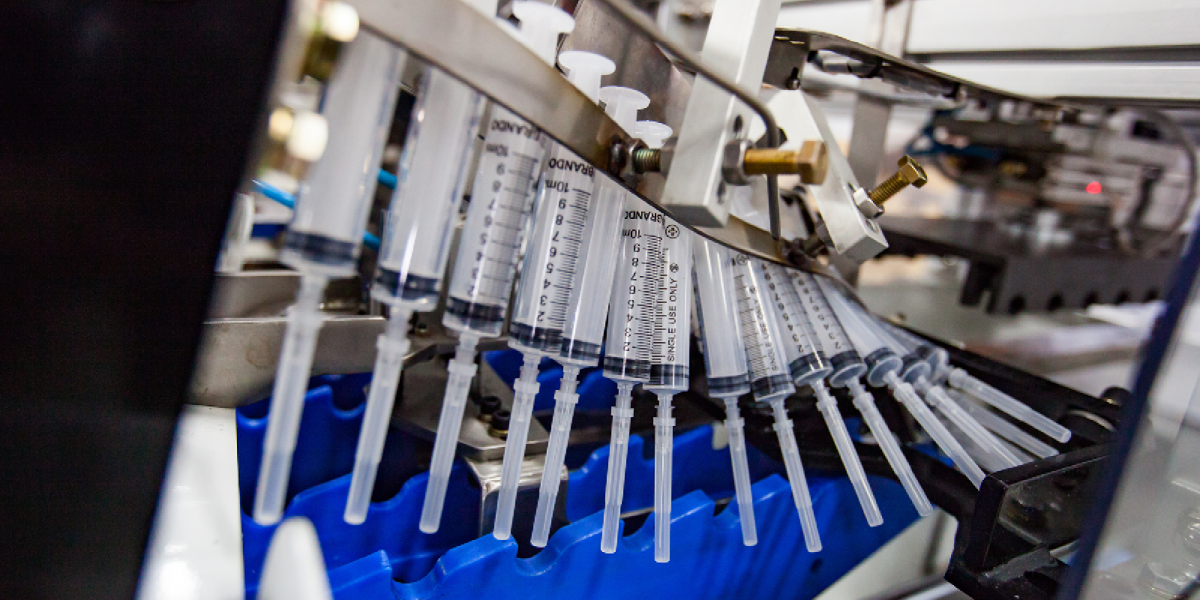
Four Scores…
When ascertaining whether or not a mechanical, electrical, and plumbing (MEP) engineering firm can properly meet the significant and specialized needs of an industrial project, there are four main tenets that are critical for success: Responsiveness, sanitation, safety, and adaptiveness. Selecting an MEP firm that has the necessary knowledge and experience to provide a high-performing space can lead to the creation of plants, factories, laboratories, and other industrial projects that have less major/critical shutdowns, lower insurance premiums, a decrease in jobsite accidents, and lower utility consumption. Furthermore, industrial sites that are optimized allow clients to save money due to efficiencies that lead to more production without an uptick in manufacturing costs.
Firms that are experienced in creating high-performing spaces in this industry offer a highly organized and streamlined response when presented with critical issues that could cause major plant shutdowns. They utilize design techniques and solutions that optimize work environment cleanliness, design workspaces that best mitigate risk to employees and company property, and have the necessary expertise to provide the infrastructure that can adapt to future owner-provided equipment.
Responsiveness
Industrial facility systems can go from perfect working order to the brink of critical failure in the blink of an eye due to unapparent complex interactions that occur as the systems evolve. MEP firms supporting these systems must be able to respond quickly when these issues arise.
The manufacturing and lab facility design requests that are received by MEP engineers can be presented in a variety of ways. Industrial projects can arise through the need to build a new facility, conduct a renovation, or provide an addition to ensure the facility is operating at peak efficiency. Such improvements often trigger the need to update existing facility areas to current codes, sometimes expanding the project scope significantly beyond what was initially anticipated.
Many industrial MEP design projects are initiated through the necessity to fix critical infrastructure issues, which could involve sudden equipment failures or risks that must be addressed to avoid failures. Malfunctions to a building system can cause a part of or a whole facility to shut down, which can equate to lost revenue ranging from thousands to tens of thousands for the owner, depending on the size and scale of operation. At Alvine, our industrial design specialists understand the necessity to offer solutions in a highly coordinated and expedited fashion that helps owners avoid profit loss. Frank Scalise, a project manager and a lead mechanical designer for Alvine, has 35 years of professional design experience, with a large portion dedicated to the industrial and laboratory market sector.
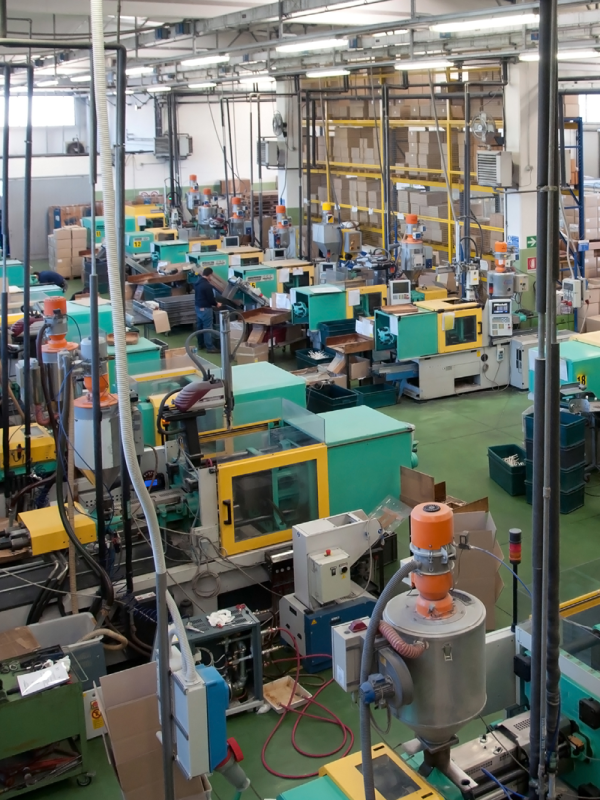
“Some of these facilities are meant to be operated 24/7,” Frank Scalise explained, “It’s imperative for our clients to stay on schedule and respond quickly to any necessary changes.”
This also requires our team to design with the existing facilities and spaces in mind as the project moves forward through the delivery phases. Whether this requires isolating construction areas with temporary walls and duct covers or designing and installing temporary HVAC systems, our experts agree that it takes extensive coordination to ensure systems in surrounding spaces stay online during repairs or improvements.
“We have to ensure that we’re not unintentionally redirecting dust and other contaminant particulates throughout the space,” Frank continued, “So that requires a lot of coordination. We may even be asked to help design the temporary systems that the construction team puts in place.”
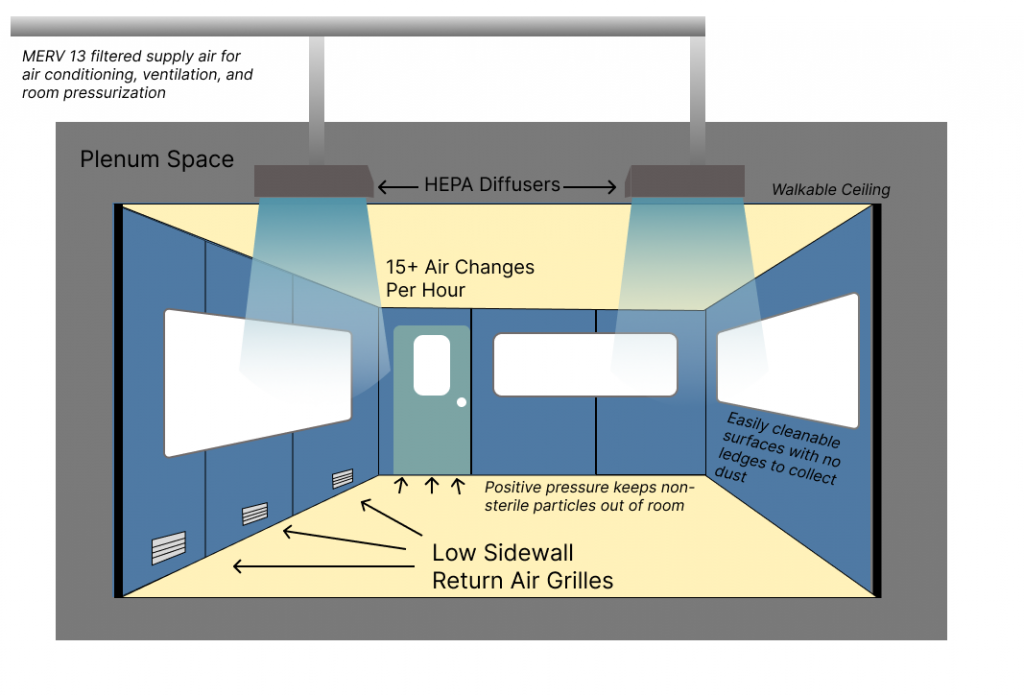
Craig and Frank have both noted a distinct increase in clientele demand involving the design and construction of clean rooms for manufacturing. More manufacturers and their customers are requiring that products be produced in a clean room environment. Designing clean rooms requires intensive attention to detail and coordination due to the intricacies of cascading pressurization design. Cascading pressurization works by designing varying levels of supply and return air, which determines whether the room contains a higher or lower pressure than its adjacent rooms. The clean room is kept with the highest level of pressure so that the cleanest air is pushed out into non-sterile adjacent spaces rather than allowing contaminated air into the sterile environment.
Our industrial team, spearheaded by Frank and Craig, routinely designs specialty building systems that are unique to research and manufacturing processes. This includes vacuum systems that can nearly replicate the vacuum of space as well as specialized chilled-water systems that cool multi-million-dollar process equipment. High-purity water production is also critical for companies producing a variety of products that are utilized in hospital and research-related industries. Similarly, clean compressed air is needed by many automated manufacturing lines to minimize equipment maintenance and ensure products are free of particulate and oil contaminants.
Sanitation
The ability of a building system’s design to support a client’s cleanliness and sanitation standards, especially when it comes to the production of medical equipment, is paramount to the success of a project. There are instances where high-purity water and/or HEPA-filtered air are integral to production, ensuring products stay sterilized throughout their assembly. Craig Johnson, a mechanical engineer and project manager, has been providing industrial facilities with mechanical systems design for nearly two decades.
“There is a lot of crossover between design principles that we utilize in laboratories and those we use in industrial facilities,” Craig Johnson explained, “The quantity and scale of the utilities within the industrial market sector is usually the big differentiator.”
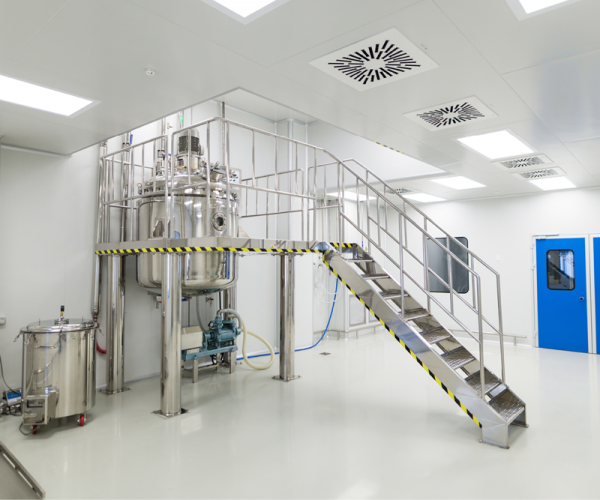
Safety
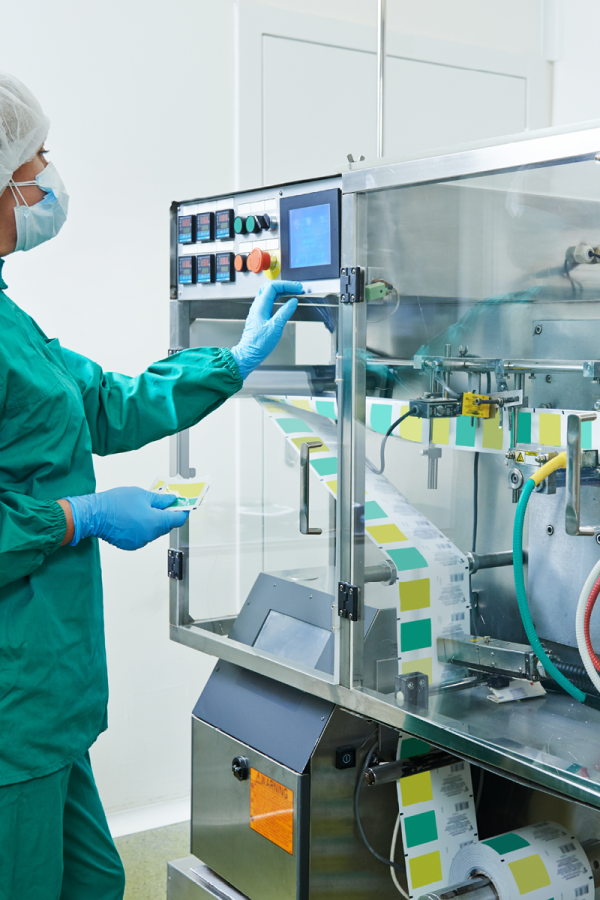
Reviewing code and process-specific safety requirements with the client and the architect is vital to the success of any industrial MEP design project. It’s no secret that our clientele wants to create a safe and comfortable environment for their employees.
“There are a lot of safety contingencies that our clients care about that go well beyond the code minimum requirements,” Frank explained, “They have employee safety to consider as well as eligibility for certain insurance premium discounts that have safety requirements; there are a lot of factors that come into play as far as safety is concerned.”
Manufacturing and industrial facilities frequently utilize hazardous chemicals. Designing to ensure chemicals can be stored safely and are contained in the event of a chemical leak/spillage is critical. Achieving high safety standards ensures our clients can run an efficient operation with fewer accidents–meaning less downtime, fewer injured employees, and a more profitable facility. Our firm’s hands-on approach to learning industry and company-specific safety standards helps owners achieve a safe environment that complies with their corporate safety initiatives, OSHA, and the requirements of their insurance carriers.
Traditionally, Alvine often acts as the prime consultant in the industrial market sector, where we have the ability to select sub-consultants and offer specialized knowledge and expertise specific to industrial MEP design needs.
“We get to put together the dream team,” Craig stated with a smile, “It’s a really unique and wonderful opportunity to be the prime on a project.”
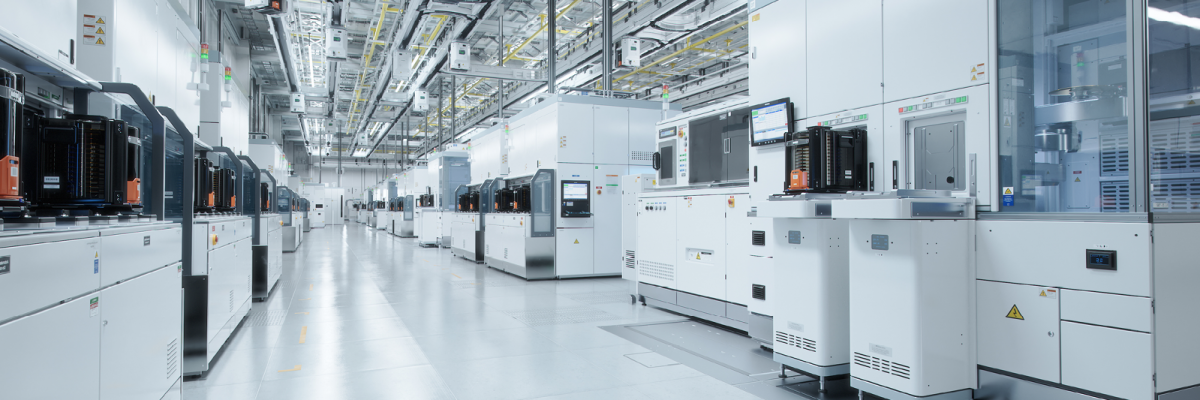
Adaptability
Our technical teams have to be ready to adapt to unknown variables when providing industrial MEP design. We are often asked to provide utility infrastructure for prototype manufacturing equipment and processing lines that have never previously been applied in the field.
“They’re almost experimental,” Frank stated, “We’re trying to gather data for the supporting utilities for machines that don’t have finished designs.”
Floor space in industrial and manufacturing facilities usually comes at a premium. Our design team can offer innovative suggestions on what is advantageous from a mechanical and electrical building system perspective on how to organize floors and machinery. However, clients have the final say on their facilities, as they know what is critical to the efficiency and profitability of their proprietary processes.
Clients could change a process equipment layout halfway through the design. Additionally, clients could decide they need additional space for future growth and renovations or cancel part of a project altogether due to a corporate program change. In order to support the client as they navigate these changes, our team keeps alternative ideas and schematics on hand to expedite the redesign process as a benefit to the owner.
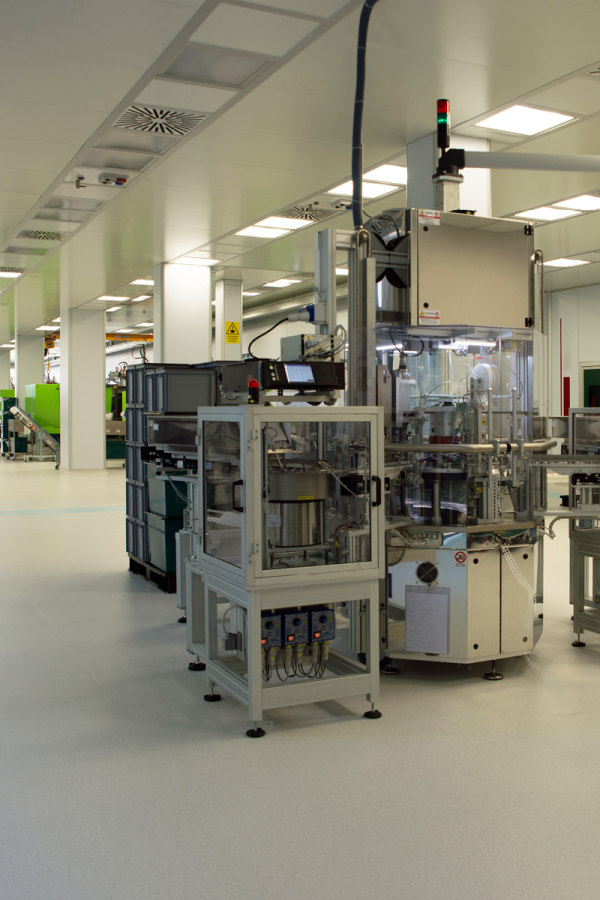
Finding The Right Team
MEP engineering teams that endeavor to create high-performance facilities, whether through renovation or new construction, are able to respond to critical infrastructure issues quickly and coherently. They are also experienced in special application building systems and designs that keep areas, machines, and products sterilized. MEP engineering teams should also have the ability to go above and beyond code requirements in order to keep operational workflows safe, efficient, and cost-conscious. Finally, owners and architects in the industrial market should collaborate with MEP engineers who have project portfolios documenting their ability to adapt to cutting-edge technology and custom process machinery.
If you’re interested in learning more about industrial MEP design, we invite you to connect with our experts for a more in-depth discussion.